作為一名生產車間管理者,應注意避免各種不必要的浪費,節約成本和資源。按照精益生產管理理論,生產現場容易哪七種浪費呢?
第一種:等待的浪費
主要因素表現為:作業不平衡,安排作業不當、待料、品質不良等。等待就是閑著沒事,等著下一個動作的來臨,這種浪費是無庸置疑的。造成等待的原因通常有:作業不平衡、安排作業不當、停工待料、品質不良等。除了在直接生產過程中有等待外,其他管理工作中就沒有等待這種浪費發生嗎?當制造部在生產新產品發生一些問題時,技術部和品質保證部是否能立即解決而不需要現場人員長時間等待?如何減少這種等待?
第二種:搬運的浪費
主要因素表現為:車間布置采用批量生產,依工作站為區別的集中的水平式布置所致。(也就是分工藝流程批量生產),無流線生產的觀念。大部分人皆會認同搬運是一種無效的動作,也有人會認為搬運是必須的動作,因為沒有搬運,如何做下一個動作?很多人都有這種想法。正因為如此,大多數人默認它的存在,而不設法消除它。有些人想到用輸送帶的方式來克服,這種方式僅能稱之為花大錢減少體力的消耗,但搬運本身的浪費并沒有消除,反而被隱藏了起來。搬運的浪費若分解開來,又包含放置、堆積、移動、整理等動作的浪費。
第三種:不良品的浪費
主要因素表現為:工序生產無標準確認或有標準確認未對照標準作業,管理不嚴密、松懈所導致。產品制造過程中,任何的不良品產生,皆造成材料、機器、人工等的浪費。任何修補都是額外的成本支出。精益的生產方式,能及早發掘不良品,容易確定不良的來源,從而減少不良品的產生。這一條比較好理解,關鍵是第一次要做正確,但實施起來卻很困難。大家不妨仔細想一想,除了產品生產,管理工作中是否也存在類似的浪費情況?精益生產方式的思想之一就是要用一切辦法來消除、減少一切非增值活動,例如檢驗、搬運和等待等造成的浪費,具體方法就是推行“零返修率”,必須做一個零件合格一個零件,第一次就做好,更重要的是在生產的源頭就杜絕不合格零部件、原材料流入生產后道工序,追求零廢品率。
第四種:動作的浪費
主要因素表現為:生產場地不規劃,生產模式設計不周全,生產動作不規范統一。要達到同樣作業的目的,會有不同的動作,哪些動作是不必要的呢?是不是要拿上、拿下如此頻繁?有沒有必要有反轉的動作、步行的動作、彎腰的動作、對準的動作、直角轉彎的動作等?若設計得好,有很多動作皆可被省掉!在管理理論中,專門有一種“動作研究”,但實施起來比較復雜,我們完全可以用上述的基本思想,反思一下日常工作中有哪些動作不合理?如何改進?
第五種:加工的浪費
主要因素表現為:制造過程中作業加工程序動作不優化,可省略、替代、重組或合并的未及時檢查。在制造過程中,為了達到作業的目的,有一些加工程序是可以省略、替代、重組或合并的,若是仔細地加以檢查,你將可發現,又有不少的浪費等著你去改善。
第六種:庫存的浪費
精益生產方式認為:“庫存是萬惡之源”,要因素表現為:管理者為了自身的工作方便或本區域生產量化控制一次性批量下單生產,而不結合主生產計劃需求流線生產所導致局部大批量庫存。庫存的損害表現有:
1、產生不必要的搬運、堆積、放置、防護處理、找尋等浪費。
2、使先進先出的作業困難。
3、損失利息及管理費用。
4、物品的價值會減低,變成呆滯品。
5、占用廠房空間,造成多余的工場、倉庫建設投資的浪費。
6、沒有管理的緊張感,阻礙改進。
7、設備能力及人員需求的誤判。
第七種:制造過多(早)的浪費
主要因素表現為:管理者認為制造過多與過早能夠提高效率或減少產能的損失和平衡車間生產力。上面提到庫存是萬惡之源,而制造過多或提早完成,在豐田則被視為最大的浪費。精益生產方式所強調的是“適時生產”,也就是在必要的時候,做出必要的數量的必要的東西。此外都屬于浪費。而所謂必要的東西和必要的時候,就是指顧客已決定要買的數量與時間。
制造過多(早)的損害表現有:
1、提早用掉費用(材料費、人工費),不能創造利潤。
2、把“等待的浪費”隱藏起來,使管理人員漠視等待的發生和存在。
3、自然而然地積壓在制品,其結果不但會使制程的時間變長(無形的),而且會使現場工作的空間變大,機器間距離因此加大,逐漸地吞蝕利潤。
4、產生搬運,堆積的浪費,使得先進先出的作業產生困難。
另附:
第一種:等待的浪費
主要因素表現為:作業不平衡,安排作業不當、待料、品質不良等。等待就是閑著沒事,等著下一個動作的來臨,這種浪費是無庸置疑的。造成等待的原因通常有:作業不平衡、安排作業不當、停工待料、品質不良等。除了在直接生產過程中有等待外,其他管理工作中就沒有等待這種浪費發生嗎?當制造部在生產新產品發生一些問題時,技術部和品質保證部是否能立即解決而不需要現場人員長時間等待?如何減少這種等待?
第二種:搬運的浪費
主要因素表現為:車間布置采用批量生產,依工作站為區別的集中的水平式布置所致。(也就是分工藝流程批量生產),無流線生產的觀念。大部分人皆會認同搬運是一種無效的動作,也有人會認為搬運是必須的動作,因為沒有搬運,如何做下一個動作?很多人都有這種想法。正因為如此,大多數人默認它的存在,而不設法消除它。有些人想到用輸送帶的方式來克服,這種方式僅能稱之為花大錢減少體力的消耗,但搬運本身的浪費并沒有消除,反而被隱藏了起來。搬運的浪費若分解開來,又包含放置、堆積、移動、整理等動作的浪費。
第三種:不良品的浪費
主要因素表現為:工序生產無標準確認或有標準確認未對照標準作業,管理不嚴密、松懈所導致。產品制造過程中,任何的不良品產生,皆造成材料、機器、人工等的浪費。任何修補都是額外的成本支出。精益的生產方式,能及早發掘不良品,容易確定不良的來源,從而減少不良品的產生。這一條比較好理解,關鍵是第一次要做正確,但實施起來卻很困難。大家不妨仔細想一想,除了產品生產,管理工作中是否也存在類似的浪費情況?精益生產方式的思想之一就是要用一切辦法來消除、減少一切非增值活動,例如檢驗、搬運和等待等造成的浪費,具體方法就是推行“零返修率”,必須做一個零件合格一個零件,第一次就做好,更重要的是在生產的源頭就杜絕不合格零部件、原材料流入生產后道工序,追求零廢品率。
第四種:動作的浪費
主要因素表現為:生產場地不規劃,生產模式設計不周全,生產動作不規范統一。要達到同樣作業的目的,會有不同的動作,哪些動作是不必要的呢?是不是要拿上、拿下如此頻繁?有沒有必要有反轉的動作、步行的動作、彎腰的動作、對準的動作、直角轉彎的動作等?若設計得好,有很多動作皆可被省掉!在管理理論中,專門有一種“動作研究”,但實施起來比較復雜,我們完全可以用上述的基本思想,反思一下日常工作中有哪些動作不合理?如何改進?
第五種:加工的浪費
主要因素表現為:制造過程中作業加工程序動作不優化,可省略、替代、重組或合并的未及時檢查。在制造過程中,為了達到作業的目的,有一些加工程序是可以省略、替代、重組或合并的,若是仔細地加以檢查,你將可發現,又有不少的浪費等著你去改善。
第六種:庫存的浪費
精益生產方式認為:“庫存是萬惡之源”,要因素表現為:管理者為了自身的工作方便或本區域生產量化控制一次性批量下單生產,而不結合主生產計劃需求流線生產所導致局部大批量庫存。庫存的損害表現有:
1、產生不必要的搬運、堆積、放置、防護處理、找尋等浪費。
2、使先進先出的作業困難。
3、損失利息及管理費用。
4、物品的價值會減低,變成呆滯品。
5、占用廠房空間,造成多余的工場、倉庫建設投資的浪費。
6、沒有管理的緊張感,阻礙改進。
7、設備能力及人員需求的誤判。
第七種:制造過多(早)的浪費
主要因素表現為:管理者認為制造過多與過早能夠提高效率或減少產能的損失和平衡車間生產力。上面提到庫存是萬惡之源,而制造過多或提早完成,在豐田則被視為最大的浪費。精益生產方式所強調的是“適時生產”,也就是在必要的時候,做出必要的數量的必要的東西。此外都屬于浪費。而所謂必要的東西和必要的時候,就是指顧客已決定要買的數量與時間。
制造過多(早)的損害表現有:
1、提早用掉費用(材料費、人工費),不能創造利潤。
2、把“等待的浪費”隱藏起來,使管理人員漠視等待的發生和存在。
3、自然而然地積壓在制品,其結果不但會使制程的時間變長(無形的),而且會使現場工作的空間變大,機器間距離因此加大,逐漸地吞蝕利潤。
4、產生搬運,堆積的浪費,使得先進先出的作業產生困難。
另附:
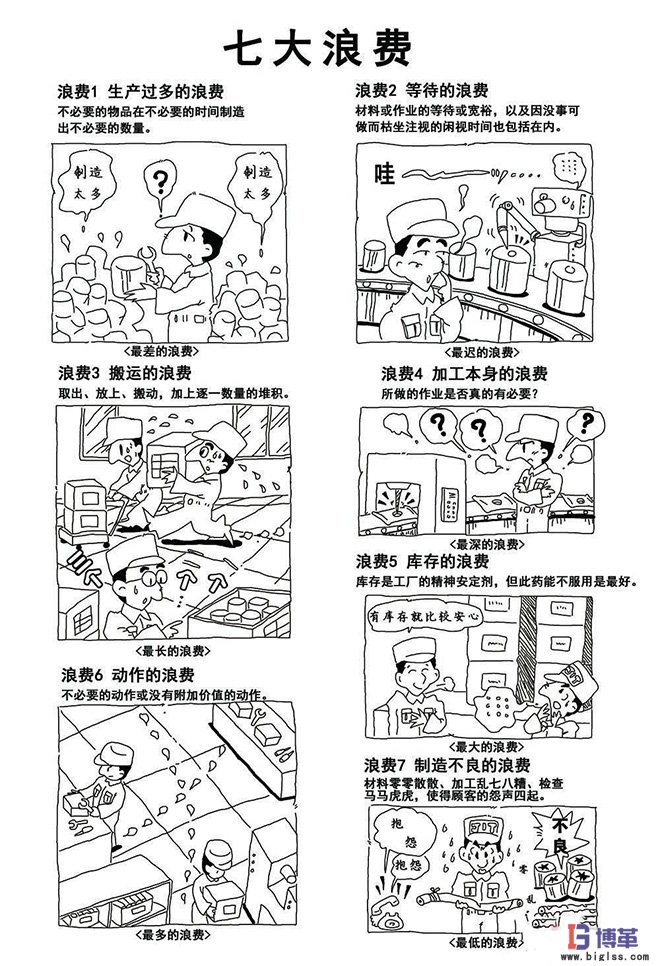
作者:博革咨詢
推薦新聞
【精美PPT】MSA測量分析系統培訓課件完整版170頁
【簡介】 本PPT 為博革咨詢精選課件-MSA測量系統實戰培訓教材,主要講述 測量系統的基本概念,測量系統分析計劃,連續和離散數據測量系統分析以及參考數據和Minitab操作案例...... 注 /about/news/down/1943.html
【精美PPT】MSA測量系統分析實戰培訓教材PPT-99頁
【簡介】 本PPT 為博革咨詢精選課件-MSA測量系統實戰培訓教材,主要講述 測量系統的基本概念,測量系統分析計劃,連續和離散數據測量系統分析以及參考數據和Minitab操作案例...... 注 /about/news/down/1942.html
【精美PPT】QFD質量功能展開培訓精編課件PPT-48頁
【簡介】 本PPT 為博革咨詢精選課件,主要講述QFD質量功能展開的概述、起源和用處,QFD展開假設的條件、QFD展開流程 、以及QFD展開的具體步驟...... 注意: 完整PPT共 48 頁,附件下載內 /about/news/down/1924.html