豐田生產方式聞名于世界,它不是對泰勒科學管理方式的照搬,而是加以改善創新,逐步形成自身獨特的一套管理模式,豐田標準化作業才用了網絡化、有彈力與創新的制度。
現代的社會環境與市場環境是,客戶需求的變化越來越快,一線員工流動率越來越高,人工成本不斷升高,動態用工和結構性用工成為必然。因此,現代企業必須保持高質量、高效率、低成本和快速應變的競爭優勢,才能在競爭中生存下來。標準化管理是應對市場新情況的最有效力式。
所謂標準化是指,為了實現整個工作過程的協調運行、提高工作效率,而對作業的質量、數量、時間、程序、方法等制定統一規定,做出統一標準,也就是對人所從事的工作標準化。
作業標準化、標準化作業、變化點管理和改善優化是標準化作業管理的動態循環。日本和美國的企業實踐證明:作業標準化做得越好,對員工技能的依賴越低,新員工上手就越快;標準化作業做得越好,生產人員越有條件進行變化點管理,一線干部越有時間推進改善優化;不斷改善和優化的結果,是使企業作業標準化體系不斷完善并得到動態維護。所以,“鐵打的營盤流水的兵”,日本和美國在華企業甚至能用高達40%以上的季節性用工,還能保持強勢的市場競爭力,標準化作業管理功不可沒。
其實,標準化作業管理由來己久,并且在19世紀中后期至20世紀初得到迅速發展。這一時期,資本主義經濟迅猛發展,然而,管理水平還很低下,仍處于經驗管理階段,工人勞動效率低、浪費嚴重,尋找一種合理有效的生產管理方式,成為亟待解決的課題。
大野耐一認為“標準化工作程序說明表及其中包含的信息是豐田生產方式中的重要組成部分。一位生產線工作者要寫出一份讓其他人能夠明白的標準化工作程序說明表,他必須相信這份說明表的必要性……避免瑕疵產品、操作失誤、意外狀況等重復發生,并納入工作者的想法,這樣才能維持高生產效率”。在這種情況下,誕生了泰勒的科學管理理論。
泰勒所走的方向是“調查影響工作的主要因素,以發現有關因素和時間之間關系的規律”。泰勒認為:“一切管理問題都應該而且可以用科學的方法加以研究,并從中優選出最好辦法,若能對其中以體系化、科學化,這種最佳辦法便可付諸實現。”
于是,在那一時期西方國家的工廠里,無論是制定勞動定額、工時定額、作業計劃還是成本核算,最后都要形成標準。因此,工作標準化在極短的時間成長、發展起來。
第二次世界大戰以后,日本積極引進泰勒制,通過制定包括工作標準在內的一系列標準,使企業管理取得顯著的效果。為日本工業的迅速復蘇做出了卓著貢獻。
可是,豐田沒有照搬泰勒的科學管理方法,而是在此基礎之上,創造性地形成了自己的管理模式。豐田認為,企業要想在所屬的行業內保持領先的地位,要有強于對手的競爭力,就必須制定出確實可行的、能授權員工的標準,只有這樣,才能持續改進重復性流程。而要充分授權員工,就必須首先把員工當作問題的解決者,而不是只知道接受命令的工具。
這樣一來,豐田把傳統企業管理中,官僚式由上而下的企業制度取消了,而采取了網絡化、有彈性與創新的制度,這就是豐田的標準化作業。
在豐田公司,標準化并不是泰勒時代的“明確寫出操作員必須遵循的工作步驟”。具體來說,豐田公司標準化作業具有以下3個特點:
1.由現場監督人員決定具體的標準作業
在以往公司,標準作業一般由IE人員來決定。而在豐田汽車公司,標準作業的各項組成要素,主要是由現場監督人員具體決定的。比如:組長、班長有權決定各臺設備生產一個單位產品需要的作業時間和各個作業人員應該完成的各種作業的順序。在制定標準作業后,組長和班長必須親自對這個標準完全掌握、了解,并且現場操作,以使作業人員可以對此標準作業完全理解、服從。
豐田認為,只有對現場作業及操作人員非常了解的人才適合作為標準作業的制定者,而班長、組長最符合這個要求。也只有這種標準作業才具有可行性、公平性,也激發了員工的主人翁意識。
2.標準化作業分為五個特定程序
(l) 確定循環時間。
(2) 確定一個單位產品的完成時間。
(3) 確定標準作業順序。
(4) 確定在制品的標準持有量。
(5) 編制標準作業書。
3.用循環時間對作業人員進行再分配
對作業人員進行再分配指的是,按生產一個單位產品所必需的不同作業數目和作業人員人數,對人員和材料進行重新分配,以減少作業流程中人員使用量。
由此看來,豐田公司的標準化并不是那種強加于員工的工作標準化,而是把標準化當作一種授權,以提高工作效率、激勵員工不斷創新。豐田標準化為企業創立了共同合作的團隊,解決了勞資關系,因而把以前被視為不利或無效的標準化,變成了有利、有效益的項目。
豐田認為,要實現持續改進,必須先把流程標準化。如果,作業流程雜亂無章法,經常改變,任何針對此流程所做的改進都是無用的。因此,豐田公司的標準化不僅僅是使作業人員的工作可重復且有效率。豐田的標準化己經應用到白領階層的工作流程中,在豐田公司任何一個角落我們都可以看到標準化的影子。
當豐田公司要開發新的產品,組織新的生產線時,是怎樣制定新的標準化的呢?比如,一個企業在一個陌生領域,要投入資金,新產品開發時,怎么把不可避免的混亂情形標準化呢?豐田公司的做法是以均衡的方式把工作標準化。當一項新產品處于早期計劃階段時,他們先把代表工廠所有部門領域的人員全部聚集在一個開放式辦公室,形成一支大團隊,稱為“先導團隊”。“先導團隊”不僅協助生產,還和工程部門攜手合作,發展最初的標準化工作,以在此產品剛推出時使用這些標準化工作,然后再把它交給生產團隊,尋求進一步改進。
在豐田公司,標準化作業的目的,是通過必要的、最小數量的作業人員進行有效生產。豐田公司的標準化,首先保證了產品的高質量。在豐田公司,當制件被發現有瑕疵時,作業人員被問的第一句話是:“有沒有按照標準化工作執行?”接著,在解決問題時,監督管理者會看著操作人員按照標準化工作說明表中規定的步驟重新執行一遍。如果發現不是操作人員的問題,他的操作完全遵循了標準化作業表,那就表示這些標準步驟必須加以修正:如果發現,是由于操作人員的執行錯誤,而導致瑕疵產品,此作業人員便會受到相應的懲罰。
實際上,豐田后一種情況發生的概率非常小。去過豐田公司的人都知道,那里的標準作業程序說明表并不是張貼在工作場所內。所有的作業人員都受過執行標準化工作的訓練,每個人都必須做到不看表一樣能準確無誤地執行標準化作業。
其次,標準化作業提高了生產率。因為,標準化讓許多無效勞動不再出現在生產作業中,既提高了工作效率,又激發了員工的工作積極性。標準化使均衡化生產成為可能,因為,在實現標準化的過程中,“循環時間”或者說均衡化理念就己經很好地貫徹到作業中了。標準化作業也有助于減少庫存浪費。標準化作業中,制品的“標準持有量”在消除多余的在制品庫存力面有潛在的力量。
現代的社會環境與市場環境是,客戶需求的變化越來越快,一線員工流動率越來越高,人工成本不斷升高,動態用工和結構性用工成為必然。因此,現代企業必須保持高質量、高效率、低成本和快速應變的競爭優勢,才能在競爭中生存下來。標準化管理是應對市場新情況的最有效力式。
所謂標準化是指,為了實現整個工作過程的協調運行、提高工作效率,而對作業的質量、數量、時間、程序、方法等制定統一規定,做出統一標準,也就是對人所從事的工作標準化。
作業標準化、標準化作業、變化點管理和改善優化是標準化作業管理的動態循環。日本和美國的企業實踐證明:作業標準化做得越好,對員工技能的依賴越低,新員工上手就越快;標準化作業做得越好,生產人員越有條件進行變化點管理,一線干部越有時間推進改善優化;不斷改善和優化的結果,是使企業作業標準化體系不斷完善并得到動態維護。所以,“鐵打的營盤流水的兵”,日本和美國在華企業甚至能用高達40%以上的季節性用工,還能保持強勢的市場競爭力,標準化作業管理功不可沒。
其實,標準化作業管理由來己久,并且在19世紀中后期至20世紀初得到迅速發展。這一時期,資本主義經濟迅猛發展,然而,管理水平還很低下,仍處于經驗管理階段,工人勞動效率低、浪費嚴重,尋找一種合理有效的生產管理方式,成為亟待解決的課題。
大野耐一認為“標準化工作程序說明表及其中包含的信息是豐田生產方式中的重要組成部分。一位生產線工作者要寫出一份讓其他人能夠明白的標準化工作程序說明表,他必須相信這份說明表的必要性……避免瑕疵產品、操作失誤、意外狀況等重復發生,并納入工作者的想法,這樣才能維持高生產效率”。在這種情況下,誕生了泰勒的科學管理理論。
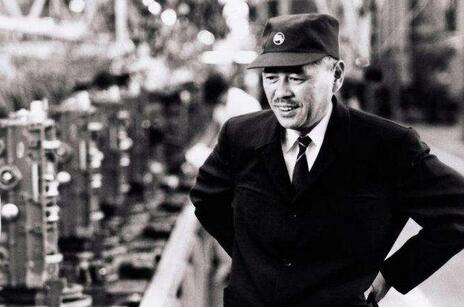
于是,在那一時期西方國家的工廠里,無論是制定勞動定額、工時定額、作業計劃還是成本核算,最后都要形成標準。因此,工作標準化在極短的時間成長、發展起來。
第二次世界大戰以后,日本積極引進泰勒制,通過制定包括工作標準在內的一系列標準,使企業管理取得顯著的效果。為日本工業的迅速復蘇做出了卓著貢獻。
可是,豐田沒有照搬泰勒的科學管理方法,而是在此基礎之上,創造性地形成了自己的管理模式。豐田認為,企業要想在所屬的行業內保持領先的地位,要有強于對手的競爭力,就必須制定出確實可行的、能授權員工的標準,只有這樣,才能持續改進重復性流程。而要充分授權員工,就必須首先把員工當作問題的解決者,而不是只知道接受命令的工具。
這樣一來,豐田把傳統企業管理中,官僚式由上而下的企業制度取消了,而采取了網絡化、有彈性與創新的制度,這就是豐田的標準化作業。
在豐田公司,標準化并不是泰勒時代的“明確寫出操作員必須遵循的工作步驟”。具體來說,豐田公司標準化作業具有以下3個特點:
1.由現場監督人員決定具體的標準作業
在以往公司,標準作業一般由IE人員來決定。而在豐田汽車公司,標準作業的各項組成要素,主要是由現場監督人員具體決定的。比如:組長、班長有權決定各臺設備生產一個單位產品需要的作業時間和各個作業人員應該完成的各種作業的順序。在制定標準作業后,組長和班長必須親自對這個標準完全掌握、了解,并且現場操作,以使作業人員可以對此標準作業完全理解、服從。
豐田認為,只有對現場作業及操作人員非常了解的人才適合作為標準作業的制定者,而班長、組長最符合這個要求。也只有這種標準作業才具有可行性、公平性,也激發了員工的主人翁意識。
2.標準化作業分為五個特定程序
(l) 確定循環時間。
(2) 確定一個單位產品的完成時間。
(3) 確定標準作業順序。
(4) 確定在制品的標準持有量。
(5) 編制標準作業書。
3.用循環時間對作業人員進行再分配
對作業人員進行再分配指的是,按生產一個單位產品所必需的不同作業數目和作業人員人數,對人員和材料進行重新分配,以減少作業流程中人員使用量。
由此看來,豐田公司的標準化并不是那種強加于員工的工作標準化,而是把標準化當作一種授權,以提高工作效率、激勵員工不斷創新。豐田標準化為企業創立了共同合作的團隊,解決了勞資關系,因而把以前被視為不利或無效的標準化,變成了有利、有效益的項目。
豐田認為,要實現持續改進,必須先把流程標準化。如果,作業流程雜亂無章法,經常改變,任何針對此流程所做的改進都是無用的。因此,豐田公司的標準化不僅僅是使作業人員的工作可重復且有效率。豐田的標準化己經應用到白領階層的工作流程中,在豐田公司任何一個角落我們都可以看到標準化的影子。
當豐田公司要開發新的產品,組織新的生產線時,是怎樣制定新的標準化的呢?比如,一個企業在一個陌生領域,要投入資金,新產品開發時,怎么把不可避免的混亂情形標準化呢?豐田公司的做法是以均衡的方式把工作標準化。當一項新產品處于早期計劃階段時,他們先把代表工廠所有部門領域的人員全部聚集在一個開放式辦公室,形成一支大團隊,稱為“先導團隊”。“先導團隊”不僅協助生產,還和工程部門攜手合作,發展最初的標準化工作,以在此產品剛推出時使用這些標準化工作,然后再把它交給生產團隊,尋求進一步改進。
在豐田公司,標準化作業的目的,是通過必要的、最小數量的作業人員進行有效生產。豐田公司的標準化,首先保證了產品的高質量。在豐田公司,當制件被發現有瑕疵時,作業人員被問的第一句話是:“有沒有按照標準化工作執行?”接著,在解決問題時,監督管理者會看著操作人員按照標準化工作說明表中規定的步驟重新執行一遍。如果發現不是操作人員的問題,他的操作完全遵循了標準化作業表,那就表示這些標準步驟必須加以修正:如果發現,是由于操作人員的執行錯誤,而導致瑕疵產品,此作業人員便會受到相應的懲罰。
實際上,豐田后一種情況發生的概率非常小。去過豐田公司的人都知道,那里的標準作業程序說明表并不是張貼在工作場所內。所有的作業人員都受過執行標準化工作的訓練,每個人都必須做到不看表一樣能準確無誤地執行標準化作業。
其次,標準化作業提高了生產率。因為,標準化讓許多無效勞動不再出現在生產作業中,既提高了工作效率,又激發了員工的工作積極性。標準化使均衡化生產成為可能,因為,在實現標準化的過程中,“循環時間”或者說均衡化理念就己經很好地貫徹到作業中了。標準化作業也有助于減少庫存浪費。標準化作業中,制品的“標準持有量”在消除多余的在制品庫存力面有潛在的力量。
作者:博革咨詢
推薦新聞
蘇州礦山機械領軍企業精益改善優秀成果展現
博革于2021年10月正式與蘇州創力達成合作,簽署精益布局項目,旨在全面改造升級齒輪車間,歷時4個月完成前期規劃,另根據規劃項目歷時1年改造完成,現新車間已經投入使用,并且達到預期目標。 /news/4855.html
博革攜手江東金具設備制造,精益咨詢管理改善促生產
江東金具決定與上海博革咨詢達成協議:由上海博革咨詢為江東金具進行工廠布局規劃和目視化設計工作。項目定位為打造絕緣子行業國內領先、行業標桿的智能化、自動化燈塔工廠。 /news/4866.html
國內PPE行業領軍企業賽立特園區精益布局
博革自2022年起為賽立特提供精益管理服務,助力企業搭建精益管理體系,推動精益化管理落地見效,從而全面轉型升級,提升企業競爭力。本次項目從2024年10月進駐,經過調研分析,圍繞園區整布局 /news/4864.html