一、某汽車零部件公司生產現狀
某汽車零部件公司為提高職工的生活水平,每年進行調薪并提供各種福利。近幾年隨著國際能源價格的走高。原材料價格也持續提高,但該公司產品價格沒能同步反應,這導致該公司運營成本上升,利潤率降低。共次在產品上的競爭愈演愈烈,導致該公司爭取新業務時需要更具競爭力的價格,更加影響了本已不多的利潤空間。
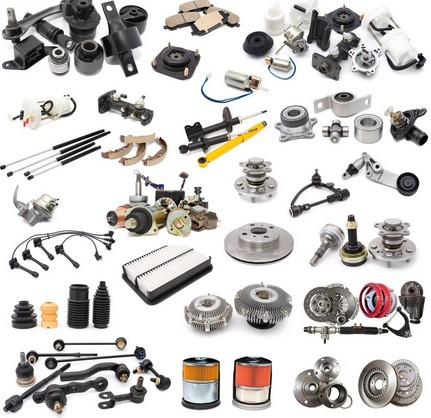
利潤空間的減少需要通過節約運營成本,提高生產效率來加以彌補。
通過該公司的調查發現其主要面臨以下問題:
1、生產方式落后,統一下發生產計劃進行推動式生產使各車間成為“孤島”。現場、庫房存在大量庫存,占用大量空間和資金,同時帶來質量隱患;
2、設備管理粗放,很少關心設備利用率,設備停機、換模時間較長;
3、現場管理松散,生產效率低。
該公司要想生存和發展就必須開始進行持續改進和成本控制,要達到這一目的該公司需要優化調配人員、設備、資金等資源,使它們發揮最大效益。“沒有一個國家可以在低廉的工資基礎上在全球競爭中建立長時間的絕對優勢,但可以通過精益生產和精益理念來維系優勢”。
二、該公司精益生產改善方案
借助價值流圖析法分析,價值流是當前產品通過其基本生產過程所要求的全部活動。這些活動包括增加價值和不增加價值兩部分,簡單地說包括從供應商到工廠制造再到顧客交付的過程。
首先確定實施精益生產方式的產品線,然后對選取的產品線進行研究。收集數據,繪制現階段的價值流程圖。通過對現有價值流程圖的分析,找到需要改進的地方并運用精益的改善工具提出改進方案。繪制未來改進后的價值流程圖,實施精益生產方式,驗證改進效果。
通過對該公司精益生產的探索和研究,共對打公司的生產管理方式做了如下改善:
1、目視化管理
為了更方便的掌握生產情況,對該公司進行目視化管理。設立控制中心,將需要的信息集中展示。按照管理層級的不同將控制中心分為:生產單元控制中心、工廠控制中心,運營控制中心。除此之外使用不同顏色定義標識的種類,對關鍵的生產控制要素進行顏色標準化管理。
①生產單元控制中心
在各車間設立生產單元控制中心進行目視化管理。控制中心的展示板上需要展示每班生產計劃完成情況、一次通過率、人員培訓矩陣、安全通報、客戶抱怨信息等內容。通過控制中心,管理者來到現場后可以對車間的生產、質量、安全情況一目了然。可以對問題立即采取行動。
②工廠控制中心
工廠控制中心可以使管理者清楚所有重要指標的達成情況。工廠控制中心包括異常發運、產量、容戶投訴、審核結果、持續改進等。在這里管理層可以直接了解工廠的各方面情況,為制定工作計劃提供依據。
③運營控制中心
運營控制中心包括該公司各部門的管理信息,是對各項業務、部門管理狀態的展示。同時通過運營中心。管理者可以掌握公司的財務情況,銷售情況。
④顏色標識標準化管理
通過定義各種顏色的使用范圍,給工廠內部的現場管理和標識提供一個統一的標準。顏色使用范圍定義如下:
黃色:防錯夾具、工裝
紅色:不合格品存放區域、器具
粉紅:特殊操作指導,如質量警報
紫紅:在制品存放區域、器具
深綠:員工培訓狀態
薰衣草色:量具存放區域、器具、校準標簽
淺綠:過程點檢表
橙色:邊界樣件存放區域、邊界樣件
淡藍:首件存放區域、換型點檢表
白底黑字:操作指導書
白底藍字:質量控制點
通過目視化管理使車間的現場管理人員和公司管理層清楚他們的職責和工作日標,使他們選徉正確的行動方向、做正確的決定。同時讓員工理解工作要點和工作環境的重要性。將生產請況和表現用簡單的方式展現出來,暴露出問題,并迅速開始解決問題,減少了反應時。
2、使用看板進行拉動式生產
該公司根據看板的使用要求實施了拉動系統來進行生產。在發泡車間設置了超市,并使用信號看板控制生產。在縫紉車間使用工序內看板。在縫紉和縫制車間、縫制和裝配電檢車間使用了工序間拉動看板進行拉動式生產。
通過實施拉動式生產,該公司減少了大量在制品庫存。節約了下廠的空間面積,減少了生產制造周期。
3、全面生產維護
全面生產維護,其目的是致力于建立一套全員參與體系使生產系統的總體效率最大化。主要特點在“全員”和“維護”。“全員”指全員參與,“維護”體現在預防維護,即發生問題之前進行維護,消除問題隱患。
該公司進行了全面生產維護活動,根據設備的特點和使用頻率制定出設備維護計劃。維護計劃又根據實施的人員和實施的頻次進行分級,共分為三級。
一級維護由現場的操作者完成,維護內容最簡單,主要在生產起始點和生產結束時進行。維護頻次最高。每個班都需要進行;
二級維護由維修部技師和工程師來完成,維修內容相對復雜。維修頻次在每個月進行一次;
三級維護由維修部門工程師來完成,維護內容最復雜,有時需要更換備件。維護頻率為三個月一次。
對生產設備都建立了維護檔案,包括各級維護計劃,維護保養操作指導,維護保養點檢清單等管理文件。通過制定并執行分級維護保養,使生產線設備能夠處于最佳運作狀態,減少設備的故障次數。
為了達到良好的效果,公司還制定了全面生產維護的培訓計劃,對參與維護的人員給予充分的培訓。在培訓活動中經驗豐富的技術人員給一線的員工講解設備工作原理、防錯裝置、管線氣路,同時互相交流經驗,提升了全員的維護技能和水平。
為了便于管理,公司成立了全員維護控制中心。控制中心用關鍵指標來監控維護活動的進展情況,這些指標包括:停機時間及原因分析、維修金額、培訓計劃執行情況、設備維護保養執行情況等。
4、應用快速換模技術
該公司發泡車間包括3條生產線,共14個發泡箱。發泡模具更換較頻繁平均每個發泡箱每天更換1次模具。每次更換模具需要1小時時間,其中包括半小時模具的更換安裝,半小時的模具預熱。隨著產量的上升,產能顯得日趨緊張,迫切需要減少模具的換模時間。
產品換型主要包括模具更換和程序更換。模具更換包括將舊模具從模架上卸下,將要使用的模具安裝到模架上,連接出料管,預熱等步驟。程序更換需要在設備控制面板選擇相應的生產程序。
具體分析:
①將換模過程進行錄像,對各步驟進行觀察分析,記錄每個過程所用的時間,同時觀察并記錄操作者在過程每個階段的行走路線及時間,對數據進行分析。通過分析,區分出外部作業和內部作業。
②對內部作業進行觀察,找到可能轉變為外部作業的部分。同時使用輔助工具或重組作業流程將部分內部作業轉化成外部作業。操作人員必須在設備運行中完成所有的外部作業,一旦設備停下來則應集中全力于內部作業。
經過觀察,換模后的模具預熱部分可以由內部作業轉化為外部作業,即在換模之前就將模具進行預熱,使模具達到要求的溫度,在安裝完畢后可以直接進行發泡生產。這樣由之前在模架上預熱變為線外預熱,可以節省預熱時間30分鐘。
③持續改進,減少外部作業時間和內部作業時間。定期召開專題會議,討論減少換模時間的方法。
5、現場5S管理的改善
5S管理是精益生產方式的基礎,為了加強5S的管理,對該公司加強生產現場清潔、清理的管理,使現場整潔干凈、秩序井然。在工具存放處進行定置定位管理,使工具使用情況一目了然。為了使車間工作環境能夠徹底改善,在車間增加了綠植,并更換了吸塵設備使工作環境得到改善。