TPM推進過程中標準化的作用
日期:2016-12-02 / 人氣: / 來源:www.600668.net / 熱門標簽:
歡迎您訪問博革咨詢官網!博革咨詢是中國首家整合精益生產/六西格瑪/流程再造的咨詢公司,專注于提供 精益生產、6S現場管理、TPM設備管理、精益工廠布局、專業目視化、精益供應鏈、精益研發、六西格瑪管理、智能制造等綜合性問題解決方案并負責落地實施。
全國咨詢熱線:021-62373515、157-2153-3189
我們承諾:見效快、易復制,目標必對賭!
TPM是以提高設備綜合效率為目標,以全系統的預防維修為過程,全體人員參與為基礎的設備保養和維修管理體系。那么TPM該如何推進呢?TPM推進過程中標準化的作用又是什么呢?
俗話說“工欲善其事,必先利其器”,在企業中設備是制造產品,創造附加價值的利器,是企業生產運行的重要資源。設備的良好狀況、利用狀況和設備的運行效率是企業生產管理的重要課題。如何使設備在兼顧生產、保養及維修等多方面的共同滿足?
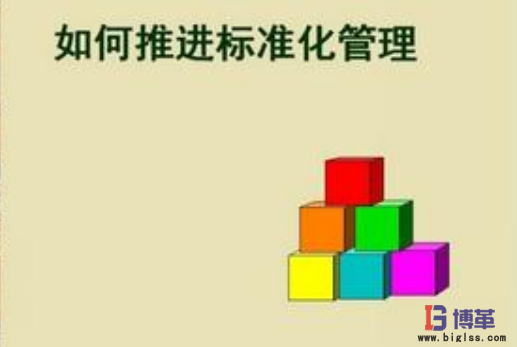
TPM強調五大要素,即:
——TPM致力于設備綜合效率最大化的目標;
——TPM在設備一生建立徹底的預防維修體制;
——TPM由各個部門共同推行;
——TPM涉及每個雇員,從最高管理者到現場工人;
——TPM通過動機管理,即自主的小組活動來推進。
其具體含義有下面4個方面:
1.以追求生產系統效率(綜合效率)的極限為目標;
2.從意識改變到使用各種有效的手段,構筑能防止所有災害、不良、浪費的體系,最終構成“零”災害、“零”不良、“零”浪費的體系;
3.從生產部門開始實施,逐漸發展到開發、管理等所有部門;
4.從最高領導到第一線作業者全員參與。
TPM活動由“設備保全”、“質量保全”、“個別改進”、“事務改進”、“環境保全”、“人才培養”這6個方面組成,對企業進行全方位的改進。
成功實施TPM的公司很多,其中包括許多世界馳名公司,如:福特、柯達公司等,他們關于TPM的實施報告都說明了自從公司實施TPM后,生產率有顯著提高,如柯達公司,它聲稱公司采用TPM技術后,獲得了500萬比1600萬的投入產出比;另一家制造公司則稱其沖模更換時間從原來的幾小時下降到了20分鐘,這相當于無需購買就能使用兩臺甚至更多的、價值上百萬美元的設備。美國德州州立大學聲稱通過研究發現,在某些領域采用TPM可以提高其生產率達80%左右,而且這些公司均聲稱通過TPM可以減少50%甚至更多的設備停機時間,降低備件存貨量,提高按時交貨率。TPM管理已經成為世界級的制造管理技術。
筆者在實施TPM管理的過程中,經過不斷探索和總結,發現標準化這一工具能夠在TPM管理中起到非常重要的工作,為企業的管理夯實了基礎,具體表現如下所述。
案例實施背景介紹:
公司為民營大型化工企業,設備已經投入運行了一段期間,從實地調查信息反饋來看,大部分設備處于青壯年期, 1條新投產的生產線處于磨合期,自動化程度高,大部分設備處于穩定運行狀態,設備的年維護費用處于穩定下降狀態,員工隊伍比較穩定,而且企業的維護人員對于設備保全這一環節也已經積累了相當的經驗,已經初步建立了一套詳實并有效執行的設備管理規章制度。
案例實施過程介紹:
筆者所在團隊進入該公司進行TPM咨詢時,首先是進行了5S管理,通過現場推進5S,整理了現場的多余物品,對于現場保留的材料,通過定位、定容、定量的整頓,有效的提高了現場管理效率,這也是我們在推進TPM管理之初,所需要達到的基本管理要求,此時我們開始為企業導入TPM管理。
首先對于設備維護具體對象,通過調查,依據當前設備的不同狀態,設立針對性極強的維護方案,避免一刀切的粗放式管理。
其次,通過標準化管理,設立了如下步驟:
一、6源的找尋與解決
6源主要涵蓋生產過程中設備管理的6個細節方面,通過整個作業現場6源的改善,培養員工能夠自主發現問題、分析問題和解決問題的能力,達到減少80%的設備維護工作量,推進TPM工作深化開展的目的。
在6源內我們還將繼續深入各自的6個源頭,由于篇幅所限,先舉故障源的深入為例。
故障源在整個企業生產活動中可以細分為5個大類:
A、設備的固有故障,這主要指的是設備的先天不足,設計缺陷、制造質量缺陷、原材料缺陷等;
B、操作不當故障源,主要分3類,第一類是員工未按操作規程操作,出現誤動作;第二類是編程失誤、參數調整失誤、指令失誤等;第三類是對于設備的過載操作;
C、維護不當故障源,主要是設備缺乏常規的清掃、點檢、保養、潤滑;
D、維修不當故障源,因為缺乏維修工藝、規范或維修工藝不合理引起的損壞維修、過維修;或者是維修操作失誤、未能執行維修工藝要求而造成的損壞維修,如零件的安裝錯位、緊固不當(過緊或過松)、線路接反、短路等等,嚴重的維修不當使一些零件不能安裝到位,出現結構缺件;
E、自然劣化故障,主要是設備性能的自然劣化導致,如自然磨損、材料老化。
二、設備效率化個別改善的實施
通過前期對于6源的找尋與解決,針對部分難以解決的6源,采取專業維護人員和機臺操作人員共同組成的小組技改活動來完成,通過小組活動,OPL、4M分析等等相關管理工具的使用,輔之以成果發布會,獎勵等多種形式,達到最終設備效率化的提升。
三、設備使用部門自主保養體制的建立
由于設備維護管理過程中,80%的問題都是與日常機臺設備操作不當有關,所以建立部門自主保養體制就是整個TPM推進落實的關鍵之處,只有讓員工能夠自主維護管理這些80%的細小問題,這樣對于企業設備管理部門就可以節省出大量的精力,來解決剩下的20%的重大設備問題,將有限的精力從日常的細節瑣碎的保養活動中解放出來,集中到重大設備管理保養維護等活動中去。
四、設備管理維護標準化的深入落實
從世界500強企業,特別是以日本為代表的制造企業的發展過程來看,成功的管理就是細節管理,再往深處看,就是維持和改進標準規范的嚴格性非常強,標準和規范不是對人的控制,而是對過程的控制,通過對與過程的控制和標準化,達到有效操作的迅速復制和推廣,從而迅速提高生產力。
在日常工作過程中,員工的每天工作,不是做對了就是出現異常,做對了,就是說明員工維持原有的標準和規范是有效的。出現異常,主要是2類原因,目前企業中大部分是員工對于原有標準和規范的執行不到位、不徹底甚至偏離,這個占統計數據的95%以上,當然另外一類原因是原有的標準已經不適應企業生產發展的需求,需要重新改善制訂標準,這種狀況根據統計往往只有5%而已。
在整個TPM推進過程中,我們非常注意標準化在管理中的應用。通過標準化,我們可以將企業在TPM推進過程中的經驗和教訓都全部保存下來,避免由于人員更替導致設備的維護履歷的丟失。在推進過程中,我們主要建立以下標準化過程:
1、設備維護技術管理標準化:
主要涵蓋維護工藝、手段和技術方案
2、維護標準規范化:
維護技術、點檢、潤滑(給油脂)、維護作業標準
3、運行/維護/維修流程標準化:
1)操作員工的操作、運行和設備維護流程;
2)設備檢維護人員的設備維護流程;
3)設備檢修計劃流程;
4)設備技術改造流程;
5)設備安全檢查流程;
6)故障維修請求和緊急處理流程。
4、維護行為標準化:
1)設備解體檢查和故障診斷;
2)設備主要總成、部件和零件的修理規范;
3)設備修復裝配;
4)設備試車檢驗;
5)設備移交生產驗收;
6)設備維修操作程序。
通過以上這些細致的標準化管理的落實,達到TPM的真正核心推進目的。
五、職能部門計劃保養體制的建立
對于設備維護管理部門,我們是通過以下行為來建立計劃保養體制:
1) 按照設備磨損老化狀況分為初始故障期、偶發(隨機)故障期、和耗損故障期3個階段,并分別設立維護對策;
2)依據設備磨損狀況制訂具體的設備維護體系的策略要點
3)建立設備維護體系的10種日常維護模式
事后維護、周期性預防維護、狀態預知維護、點檢定修、改善維護、主動維護、以可靠性為中心的維護、以利用率為中心的維護、風險維護、預定翻新和預定報廢
4)維護策略的優化選擇,根據設備故障特性、設備停機損失、設備故障后果、 設備故障預防和排除費用等要素進行總體全面優化選擇
六、設備操作、保養技能提升的培訓
七、軟件在TPM管理中的使用
由于企業規模日益擴大,自動化程度的日益提高,傳統的人工管理設備保全已經有些力不從心,設備的信息化管理成為我們在TPM推進中需要解決的事項。
首先通過細致定義設備磨損狀況,結合行業特點,我們制訂了具體的設備維護體系的策略,對于設備的10種維護策略進行一一對應的定義,不同的設備對應不同的維護策略,如事后維護、周期性預防維護、狀態預知維護、點檢定修、改善維護、主動維護、以可靠性為中心的維護、以利用率為中心的維護、風險維護、預定翻新和預定報廢。
然后根據設備故障特性、設備停機損失、設備故障后果、 設備故障預防和排除費用等要素進行維護策略的總體全面優化選擇,因為原始工作量巨大,所以在實際推進過程中,先從關鍵設備機臺開始工作,抓住瓶頸部分,有重點的完成,最后在完成全部工作。
對于軟件的功能,我們要求了以下基本點:
1、設備操作人員從點檢開始的規范化,通過系統控制,強制點檢;
2、對設備故障發生時間和次數進行記錄和統計,分析設備故障發生周期,從而實現設備各系統、部位、零件等的點檢周期預測,便于預防維修的準確實施;
3、以機臺為單位的故障統計報表輸出功能,加強了對機臺操作人員、檢修作業人員的績效考核;
4、設備維護標準化規范化流程的控制,操作人員輸入故障類型時,就可以通過在系統內的設置,自動告之維護人員應該選取哪些維護方案、維護流程,同時可以達到信息的在線審批和迅速傳遞,以減少管理過程中的人為跑流程跑手續跑簽字現象,減少浪費,提高效率;
5、設備故障的描述更為簡潔、準確和實用;
6、在設備維護部門處,我們要達到很強的統計編輯功能,設備故障任意時間段內的故障時間和次數統計、故障機臺排名、故障頻次排名、各類統計報表、圖表的打印和輸出,實現設備故障周期統計及報表功能。通過報表我們能夠做好設備的預防維護工作,做到防患于未然;
7、對于設備備品備件的庫存控制,我們要求根據前期數據統計,能夠有安全庫存控制的進行庫存控制,從而在不影響維護效率的前提下,盡可能的減少備品備件庫存,減少企業成本支出。
通過以上這些標準化措施的有效實施,該公司的提升數據為設備綜合效率?提升至1.5-2倍突發故障件數減少至 為原先的5%-10%,品質不良率減少至 20%,維護成本持續有效降低,減少了30%......從數據的分析可以看出:目前該公司TPM管理已經取得了顯著成效,達到了項目咨詢的最初期待,我們相信標準化將在日后的TPM中將發揮越來越重要的作用。
作者:博革咨詢
咨詢采購表
精益生產怎么做?六西格瑪咨詢怎么做?項目周期是多少?大概需要多少費用?
我是什么企業?目前需要解決的問題是什么?預算周期是多少?想要達到什么效果?
歡迎您瀏覽博革咨詢官方網站!我們專注于精益生產咨詢、六西格瑪咨詢、精益供應鏈咨詢、5S6S現場管理、TPM設備管理咨詢、工廠布局規劃、目視化看板設計等領域的落地咨詢;若對本頁面內容不感興趣或想了解更多與您企業、行業相關的資訊,可通過以下方式尋找解決方法:
(1)工作時間可撥打我們的全國咨詢熱線:15721533189,021-62373515 進行咨詢;
(2)在網站欄目右側“搜索框” 輸入您感興趣的關鍵詞,搜索相關內容;
(3)點擊左側“在線咨詢”按鈕, 您可以和我們的專家老師在線咨詢;
(4)非工作時間請點擊網站下方的“留言” 按鈕,留下您的聯系方式和需要咨詢的內容,我們將安排專業顧問給您解答;
(5)入群方式:掃描左圖二維碼,添加小博微信好友,通過認證后,加入精益生產VIP會員微信群。
熱銷課程 Hot
相關內容 Related
- TPM設備改善如何切入?03-22
- TPM管理推行感想01-23
- TPM推進過程中的“矛”與“盾”01-23
- TPM推進心得體會01-22
- TPM管理推進感想01-22
- 2017年TPM管理三大維度推進心得01-21