部件生產周期與進度管控
在汽輪機企業有個說法:三大件解決了,交期也解決了。三大件就指高中壓外缸,轉軸,末級葉片;而在發電機企業:三大件指的是基座,轉軸,線圈。
這幾個大件主要涉及鑄鍛件采購,焊接,機加工,總裝;公司層面計劃部門投入大量時間來跟進關鍵件的計劃分解和生產進度組織,但往往項目還是由于這幾個大件的管控中的“”不可控“”原因而最終拖期。博革咨詢這所以將“不可控”加引號,是因為經過數據分析發現很多“不可控”的原因其實是管理制度造成的,而不是真正的意外因素,只是因為跨部門流程和職責管理的問題很難解決。
以轉軸總裝為例:在計劃層面非常細致,按裝配工序排好了每日作業內容,每天記錄進度和異常。但在實際作業中,有一個環節經常拖期,就是引線槽契的配尺寸。這個部件必須裝配到某工序后才能現場測量尺寸,然后去粗加工-外協發黑-精加工。總裝分廠希望在5天內完成。而這種處理的實際周期在8-15天,每個項目波動都比較大。經過內部修改工藝與計劃組織方式,內部周期壓縮到3天。但發黑周期不定。后來了解到供應商是按照批量處理的形式,每周生產一次,用一個大鍋進行加工。如果周二發給供應商的,周三就完成了。但如果周四發的,也要積壓到下周。發現這個情況后,與外協部門溝通,外協部門后面的解決方案是供應商答應了以后緊急件用一個小鍋發黑,正常件按原有流程用大鍋發黑。跟蹤了幾周,周期得到有效縮短。博革咨詢當時就感覺很難維持,問外協部門是否給供應商調整了費用。外協員說供應商答應的很痛快,沒提出增加費用的事情。還是按照原來的價格收費。項目結束半年后,博革咨詢詢問分廠領導是否穩定了周期,分廠領導說變化不大!有些項目的引線槽器還是要十多天才能返回!這里面涉及2個問題:1)這種小件實際上沒上生產部考核項,對外協部是沒有影響的,外協部關注度不夠;2)采購價格未考慮不同情況單獨定價,供應商偶爾加個小鍋生產是一回事,每天開了小鍋,然后每周一次大鍋生產,成本即使增加不多,也是不愿意執行。但即使外協部打算給加急費,是按部件號來分急件/非急件?還是按訂單號來區分?怎么在系統中記錄并給供應商正確付費?怎么考核供應商的交付績效?企業的供應商管理系統就沒細化,而且信息系統也不支持。
再以轉軸機加工為例,其中到某序需要導電桿配尺寸,經常發生轉軸已經加工完成但導電桿未完成的事情。最初是以為導電桿投料晚,數據分析才發現導電桿正常生產周期只要2個月,但投料可能提前3-4個月,依然延誤了交期。導電桿生產經常在進入某個分廠后停滯,原因是在這個分廠之前都是粗加工,保存容易。在這個分廠開始都是精加工,加工后的保管是問題,往往要等后序分廠來催才開始生產。這也是關鍵路徑上部件管控問題,在手工計劃模式下只能靠人跟進,根本解決方式是運行MRP,從系統生成各分廠的交付時間,基于ERP系統對各分廠進行考核。
其中核心的問題點是期量問題,轉化為LT/CT系數問題。到底什么是合理的系數?一次和一位中興背景的研發顧問聊天說到設計出圖晚導致交付拖期的問題,肖老師突然憤憤不平的說到,就是生產部門給自己留的水分過大,使勁壓研發周期。市場簽的合同交付周期緊,生產部門又不肯降周期,每次都壓迫研發部門!
其實期量中的標準工時,特別是大件的標準工時是很準確的,一根軸在精車上加工幾天,各部門是有共識的,差異點在于對排隊時間的爭議。按照博革咨詢的觀點,大件按照1.5倍,中等件按照3倍,小件按照1個工序1周可能是最符合裝備企業需求的周期管控方式。對于大件的交期還有一個影響因素,就是設備可用天數。博革咨詢見過的一些企業每個月按照28天安排,假定2-3天是設備保養或設備故障。另外一些企業只給出設備保養時間,不考慮設備故障來進行排產,最終發生設備故障影響項目交期再臨時解決。
對于大件的焊接工序,別看基座焊接整個周期100天,實際上其中任何一天滯后了基本就無法追回。可以采用網絡圖的方法找出最短路徑,設定正常生產周期和趕工時的生產周期。當執行過程中發生滯后立刻采用趕工的方法追回周期。
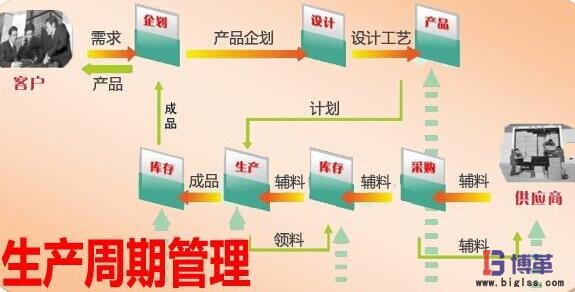
這幾個大件主要涉及鑄鍛件采購,焊接,機加工,總裝;公司層面計劃部門投入大量時間來跟進關鍵件的計劃分解和生產進度組織,但往往項目還是由于這幾個大件的管控中的“”不可控“”原因而最終拖期。博革咨詢這所以將“不可控”加引號,是因為經過數據分析發現很多“不可控”的原因其實是管理制度造成的,而不是真正的意外因素,只是因為跨部門流程和職責管理的問題很難解決。
以轉軸總裝為例:在計劃層面非常細致,按裝配工序排好了每日作業內容,每天記錄進度和異常。但在實際作業中,有一個環節經常拖期,就是引線槽契的配尺寸。這個部件必須裝配到某工序后才能現場測量尺寸,然后去粗加工-外協發黑-精加工。總裝分廠希望在5天內完成。而這種處理的實際周期在8-15天,每個項目波動都比較大。經過內部修改工藝與計劃組織方式,內部周期壓縮到3天。但發黑周期不定。后來了解到供應商是按照批量處理的形式,每周生產一次,用一個大鍋進行加工。如果周二發給供應商的,周三就完成了。但如果周四發的,也要積壓到下周。發現這個情況后,與外協部門溝通,外協部門后面的解決方案是供應商答應了以后緊急件用一個小鍋發黑,正常件按原有流程用大鍋發黑。跟蹤了幾周,周期得到有效縮短。博革咨詢當時就感覺很難維持,問外協部門是否給供應商調整了費用。外協員說供應商答應的很痛快,沒提出增加費用的事情。還是按照原來的價格收費。項目結束半年后,博革咨詢詢問分廠領導是否穩定了周期,分廠領導說變化不大!有些項目的引線槽器還是要十多天才能返回!這里面涉及2個問題:1)這種小件實際上沒上生產部考核項,對外協部是沒有影響的,外協部關注度不夠;2)采購價格未考慮不同情況單獨定價,供應商偶爾加個小鍋生產是一回事,每天開了小鍋,然后每周一次大鍋生產,成本即使增加不多,也是不愿意執行。但即使外協部打算給加急費,是按部件號來分急件/非急件?還是按訂單號來區分?怎么在系統中記錄并給供應商正確付費?怎么考核供應商的交付績效?企業的供應商管理系統就沒細化,而且信息系統也不支持。
再以轉軸機加工為例,其中到某序需要導電桿配尺寸,經常發生轉軸已經加工完成但導電桿未完成的事情。最初是以為導電桿投料晚,數據分析才發現導電桿正常生產周期只要2個月,但投料可能提前3-4個月,依然延誤了交期。導電桿生產經常在進入某個分廠后停滯,原因是在這個分廠之前都是粗加工,保存容易。在這個分廠開始都是精加工,加工后的保管是問題,往往要等后序分廠來催才開始生產。這也是關鍵路徑上部件管控問題,在手工計劃模式下只能靠人跟進,根本解決方式是運行MRP,從系統生成各分廠的交付時間,基于ERP系統對各分廠進行考核。
其中核心的問題點是期量問題,轉化為LT/CT系數問題。到底什么是合理的系數?一次和一位中興背景的研發顧問聊天說到設計出圖晚導致交付拖期的問題,肖老師突然憤憤不平的說到,就是生產部門給自己留的水分過大,使勁壓研發周期。市場簽的合同交付周期緊,生產部門又不肯降周期,每次都壓迫研發部門!
其實期量中的標準工時,特別是大件的標準工時是很準確的,一根軸在精車上加工幾天,各部門是有共識的,差異點在于對排隊時間的爭議。按照博革咨詢的觀點,大件按照1.5倍,中等件按照3倍,小件按照1個工序1周可能是最符合裝備企業需求的周期管控方式。對于大件的交期還有一個影響因素,就是設備可用天數。博革咨詢見過的一些企業每個月按照28天安排,假定2-3天是設備保養或設備故障。另外一些企業只給出設備保養時間,不考慮設備故障來進行排產,最終發生設備故障影響項目交期再臨時解決。
對于大件的焊接工序,別看基座焊接整個周期100天,實際上其中任何一天滯后了基本就無法追回。可以采用網絡圖的方法找出最短路徑,設定正常生產周期和趕工時的生產周期。當執行過程中發生滯后立刻采用趕工的方法追回周期。
作者:博革咨詢